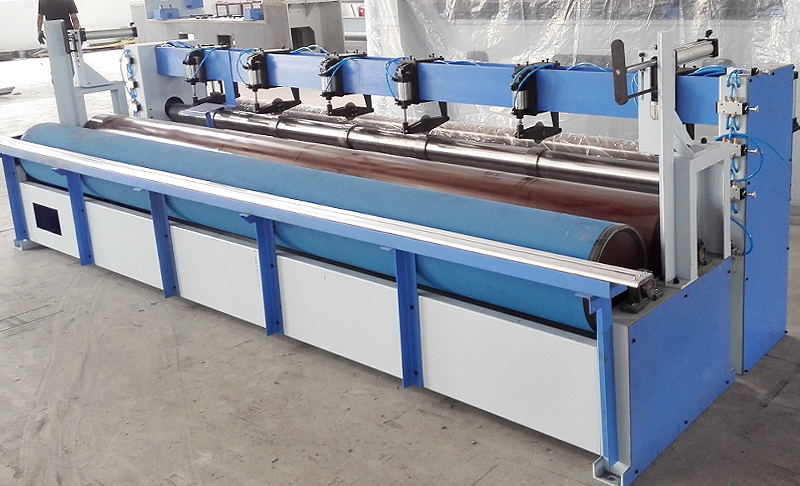
CUTTING & WINDING MACHINE | |||||
TYPE | SPECIFICATION | NOTE | |||
YBG401 | cutting width | 2600mm | 4000mm | 6000mm | for the light-weight material |
roll diameter | 320mm | 350mm | 400mm | ||
power | 0.75kw | 1.5kw | 2.2kw | ||
material weight | 50~500g/㎡ | ||||
speed | 1.5~8m/min | ||||
circular knives | three longitudinal knives + one latitudinal knife |
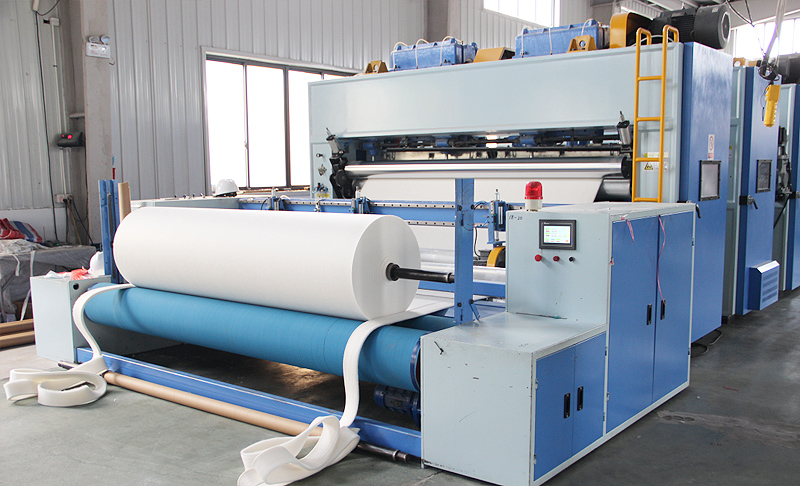
CUTTING & WINDING MACHINE | |||||
TYPE | SPECIFICATION | NOTE | |||
YBG408 | cutting width | 2600mm | 3800mm | 5200mm | for the heavy-weight material |
roll diameter | 320mm | 350mm | 400mm | ||
power | 1.5kw | 2.2kw | 3.5kw | ||
material weight | 500~2000g/㎡ | ||||
speed | 0.5~5m/min | ||||
circular knives | three longitudinal knives + one latitudinal knife |
What is it and what does it do?
Imagine you have a large roll of fabric, like the output from a production machine. Now, imagine you need to cut that large roll into smaller rolls of specific widths or lengths for packaging, distribution, or further processing. That’s what a cutting and winding machine does.
Its main job is to take a wide roll of non-woven fabric and cut it into narrower strips or rolls, while simultaneously winding these strips onto cores to create smaller, manageable rolls. Think of it as a “fabric slitter and roll maker.”
How is it done?
Cutting and winding machines use a combination of slitting mechanisms and winding systems:1
- Infeed: The large roll of non-woven fabric is loaded into the machine.
- Slitting: The fabric is then passed through a slitting section.2 This section has circular knives or razor blades that precisely cut the fabric into desired widths.3 The blades can be adjusted to produce different widths as needed.4
- Winding: After slitting, the cut strips of fabric are wound onto individual cores, creating smaller rolls.5 Each core is attached to a winding shaft, and the rotation of these shafts winds the fabric onto the cores.
- Tension Control: The machine incorporates tension control mechanisms to ensure that the fabric is wound evenly and tightly onto the cores, producing consistent rolls.
- Output: The finished smaller rolls are then removed from the machine.
Use in the Non-Woven Sector
Cutting and winding machines are essential in the non-woven industry for:
- Roll Conversion: They convert large rolls of non-woven fabric into smaller, more manageable rolls for further processing, packaging, or sale.6
- Customization: They allow manufacturers to produce rolls of specific widths and lengths according to customer requirements or product specifications.7
- Efficiency: They automate the cutting and winding process, improving efficiency and reducing labor costs.
- Variety of Products: They can be used to process various types of non-woven fabrics, including spunbond, meltblown, needle-punched, and others.
Think of it this way:
Imagine a paper towel roll. You can tear off individual towels of the desired size. A cutting and winding machine is like a machine that takes a giant roll of paper towels and cuts it into smaller rolls of different widths.
In short, the cutting and winding machine is a crucial step in converting large rolls of non-woven fabric into smaller, usable rolls.8 It’s all about efficient slitting and winding to meet product specifications and facilitate further handling or distribution of the non-woven material.