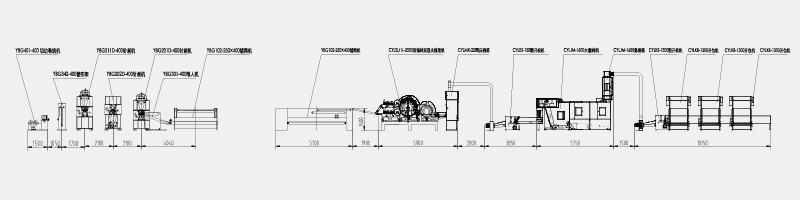
NON-WOVEN PRODUCTION LINE FOR VISCOSE THICK FELT | |||
TYPE | MAIN PARAMETER | NOTE | |
LYBG103-360 | carding output width | 3000mm | available for the materials of PSF/PHT/PPF/PPTA/ NYLON/VISCOSE FIBRE (D1.5~6.0mm/L38.0~76.0mm) |
lapping output width | 3600mm | ||
finished products width | 3200mm | ||
material weight | 80~2800g/m² | ||
production speed | 0.5~6 m/min | ||
production output | 300kg/h | ||
power capacity | 283kw |
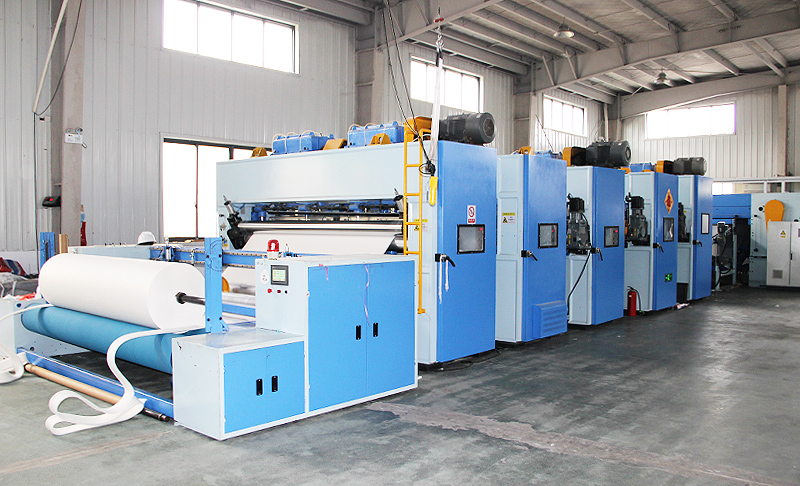
Production Line Configuration | ||||
NO. | MACHINERY | TYPE | QUANTITY | NOTE |
1 | Bale Opener | CYLKB-1300 | 2 | |
2 | Willowing Machine | CYLKS-1300 | 1 | |
3 | Willowing Machine | CYLJM-1600 | 2 | |
4 | Willowing Machine | CYLKS-1500 | 1 | |
5 | Cabinet Blending Hopper | CYLJM-2800 | 2 | |
6 | Vibrating Blending Hopper | CYLMX-2800 | 1 | |
7 | Carding Machine | CYLSL/II-3000 | 1 | |
8 | Cross Lapper | YBG101-300×360 | 1 | |
9 | Feeding Machine | YBG302A-360 | 1 | |
10 | Preliminary Needle Punching Machine | YBG241-360 | 1 | |
11 | Needle Punching Machine | YBG202D-360 | 1 | |
12 | Needle Punching Machine | YBG211D-400 | 1 | |
13 | Cutting & Winding Machine | YBG408-360 | 1 | |
14 | Control Cabinet | 1 | ||
15 | Bale Opener | CYLKB-400 | 1 | optioN |
non-woven production line designed for viscose thick felt. Let’s break down what that means and the function of each machine:
Understanding Viscose Thick Felt
- Viscose: Viscose is a semi-synthetic fiber made from cellulose (wood pulp).1 It’s known for its soft, drapable texture and is often used in textiles for its silk-like feel.2
- Thick Felt: Felt is a non-woven fabric made by matting, condensing, and pressing fibers together.3 “Thick” implies the felt will have a substantial weight and density.
The Production Line Configuration
This list details the machinery, their models, quantities, and their roles in creating the viscose thick felt.
- Bale Opener (CYLKB-1300 x2, CYLKB-400 x1 optional): This machine loosens and opens compacted bales of viscose fibers, making them fluffy and manageable for further processing. The optional smaller bale opener might be for different fiber types or smaller production runs.
- Willowing Machine (CYLKS-1300 x1, CYLJM-1600 x2, CYLKS-1500 x1): These machines further open and clean the viscose fibers, removing dust, dirt, and impurities. This step is crucial for producing high-quality felt.
- Cabinet Blending Hopper (CYLJM-2800 x2): Here, the viscose fibers might be blended with other types of fibers (if needed) to achieve specific properties in the final felt.
- Vibrating Blending Hopper (CYLMX-2800 x1): This machine ensures a homogeneous mix of the fibers before they are carded.4
- Carding Machine (CYLSL/II-3000 x1): This machine aligns the opened and blended fibers into a thin, continuous web, making them parallel and organized.
- Cross Lapper (YBG101-300×360 x1): The carded web is layered back and forth to build up thickness and width, creating a thicker, wider web.5 This is a key step in producing thick felt.
- Feeding Machine (YBG302A-360 x1): This ensures a consistent and controlled flow of the layered web into the needle punching machines.
- Preliminary Needle Punching Machine (YBG241-360 x1): This machine starts the needle punching process, lightly entangling the fibers for better handling and cohesion.
- Needle Punching Machines (YBG202D-360 x1, YBG211D-400 x1): These machines with barbed needles further entangle the fibers, creating a strong, felt-like fabric structure.6 Multiple needle punching machines allow for varying degrees of entanglement and fabric density, which directly impacts the thickness and firmness of the felt.
- Cutting & Winding Machine (YBG408-360 x1): This machine cuts the wide rolls of needle-punched felt into smaller rolls of specific widths for packaging and sale.
- Control Cabinet: This houses the electrical controls and systems to operate and monitor the entire production line.
Why Needle Punching for Felt?
Needle punching is a common method for producing felt because:
- Entanglement: The barbed needles create a strong interlocking of the fibers, resulting in a cohesive fabric.
- Thickness Control: The degree of needle punching and the layering of the web can be adjusted to create felts of various thicknesses.
- Versatility: Needle punching can be used with various fiber types, including viscose, to achieve specific properties.
Uses of Viscose Thick Felt:
Viscose thick felt has a wide range of applications, including:
- Craft and Hobby: For various craft projects, decorations, and padding.7
- Industrial Uses: For insulation, vibration dampening, filtration, and gaskets.
- Automotive: For sound absorption and interior components.
- Home Furnishings: For padding, upholstery, and rugs.8
In Simple Terms:
This production line takes raw viscose fibers, cleans and blends them, aligns them into a web, layers the web for thickness, and then uses needles to entangle the fibers into a thick, cohesive felt. Finally, the felt is rolled and cut for various uses.
This configuration allows for the efficient production of high-quality viscose thick felt with specific properties tailored to its end use. The multiple needle punching machines provide flexibility for different felt thicknesses and densities.