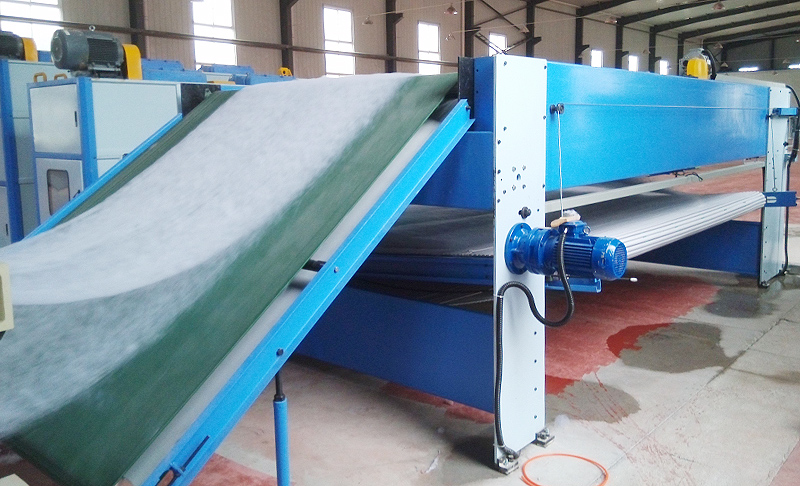
CROSS LAPPER | ||||
TYPE | SPECIFICATION | NOTE | ||
YBG102 | input width | 2000~2500mm | PLC /VFD | |
output width | 2600~8000mm | |||
speed | 10~45m/min | |||
power | 5kw |
What is it and what does it do?
Imagine you have a long, continuous sheet of paper (like the web of fibers coming out of the carding machine). Now, imagine you want to make that paper thicker and stronger by layering it multiple times, but in a criss-cross pattern. That’s exactly what a cross lapper does with the fiber web in non-woven manufacturing.
Its main job is to take the carded web and fold it back and forth, layering it onto a conveyor belt to create a thicker, wider web.1 This builds up the weight and thickness of the non-woven material.2
How is it done?
Cross lappers use a clever combination of mechanisms:
- Infeed: The carded web is fed into the cross lapper, usually from the carding machine or a preceding conveyor.3
- Folding: A series of belts or aprons move the web back and forth, folding it onto itself in a zig-zag or “S” pattern. This creates layers of fiber that are oriented at an angle (often perpendicular) to the original direction of the web.
- Layering: These folded layers are laid down onto a moving conveyor belt, building up a thicker, wider web. The speed of the conveyor and the width of the folds determine the final weight and width of the layered web.
- Delivery: The layered web, now called a “cross-lapped web,” is delivered out of the machine, ready for the next stage of the non-woven process (like needling or bonding).
Use in the Non-Woven Sector
Cross lappers are essential in non-woven manufacturing when you need:
- Increased Thickness and Weight: They allow manufacturers to create non-woven fabrics with specific thicknesses and weights by controlling the number of layers.4
- Improved Strength: By layering the web in a criss-cross pattern, cross lappers enhance the strength and dimensional stability of the non-woven material, especially in applications where strength is required in multiple directions.
- Uniformity: They create a more uniform web structure, reducing variations in thickness and density.5
- Web Formation for Specific Processes: The cross-lapped web is often an intermediate step for producing certain types of non-wovens, like those that will be needle-punched or thermally bonded.
Think of it this way:
Imagine you’re laying down strips of fabric to make a quilt. You don’t just lay them all in one direction, right? You layer them in a criss-cross pattern to make the quilt thicker and stronger. The cross lapper does something similar with the fiber web, just on a much faster and more automated scale.
In short, the cross lapper is a key machine for building up the thickness and weight of a non-woven web by layering it in a controlled, criss-cross pattern.6 It’s a crucial step in creating non-woven materials with specific properties and for preparing the web for further processing.