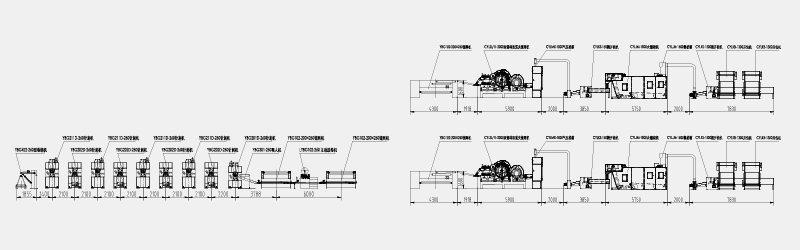
NON-WOVEN PRODUCTION LINE FOR FILTERING MATERIALS | |||
TYPE | MAIN PARAMETER | NOTE | |
LYBG103 | carding output width | 2000mm | available for the materials of PSF/PHT/PPF/PPTA/NYLON (D1.5~6.0mm/L38.0~76.0mm) |
lapping output width | 2600mm | ||
finished products width | 2300mm | ||
material weight | 80~800g/m² | ||
production speed | 0.5~6 m/min | ||
production output | 250~350kg/h | ||
power capacity | 382kw |
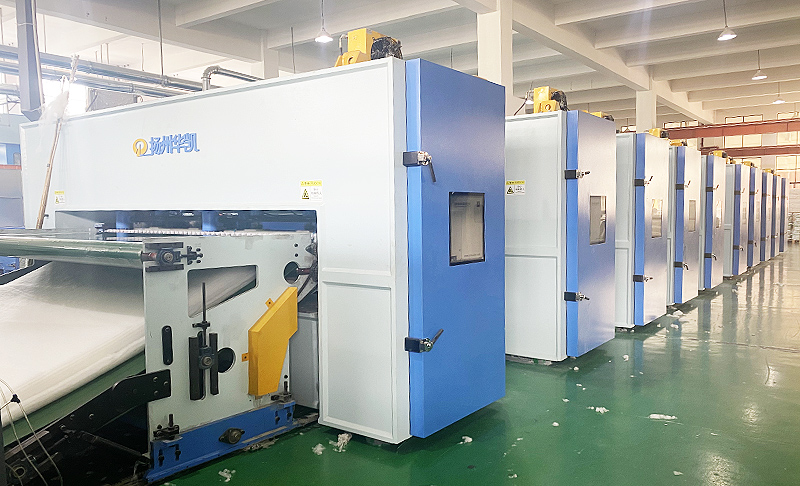
Production Line Configuration | ||||
NO. | MACHINERY | TYPE | QUANTITY | NOTE |
1 | Bale Opener | CYLKB-1300 | 4 | |
2 | Willowing Machine | CYLKS-1500 | 2 | |
3 | Willowing Machine | CYLJM-1800 | 2 | |
4 | Willowing Machine | CYLKS-1500 | 2 | |
5 | Cabinet Blending Hopper | CYLMX-1800 | 2 | |
6 | Carding Machine | CYLSL/II-2000 | 2 | |
7 | Cross Lapper | YBG102-200×260 | 2 | |
8 | Winding Machine | LYBG102-260 | 1 | |
9 | Feeding Machine | YBG301-260 | 1 | |
10 | Preliminary Needle Punching Machine | YBG201D-260 | 1 | |
11 | Needle Punching Machine | YBG202D-260 | 4 | |
12 | Needle Punching Machine | YBG211D-260 | 4 | |
13 | Cutting & Winding Machine | YBG422-260 | 1 | |
14 | Control Cabinet | 1 | ||
15 | Bale Opener | CYLKB-1300 | 1 | option |
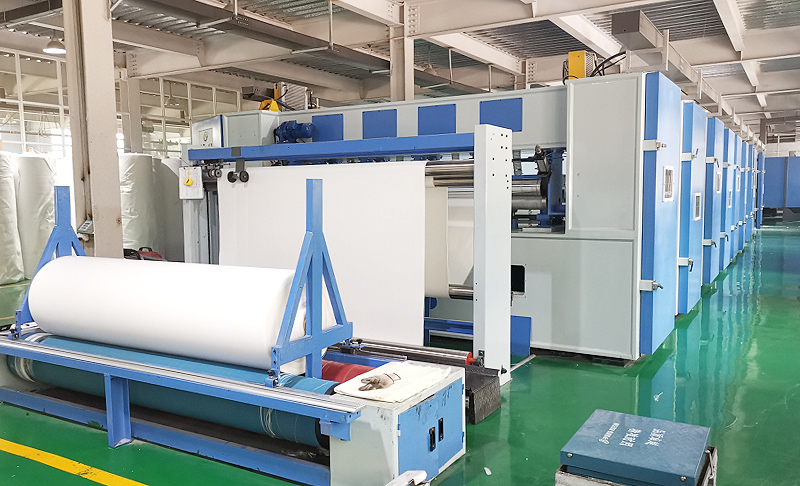
Understanding Filter Material
Filter material, in the context of non-wovens, refers to fabrics designed to separate particles from a fluid (liquid or gas) passing through them.1 These materials are crucial in various filtration applications, from air filters in your home to industrial-grade liquid filters.
The Production Line Configuration
This list outlines the machinery, their models, quantities, and their roles in creating the non-woven filter material.
- Bale Opener (CYLKB-1300 x4, CYLKB-1300 x1 optional): This machine loosens and opens compacted bales of raw fibers (likely polyester, polypropylene, or even specialized filter fibers). The optional bale opener might be for different fiber types or smaller production runs.
- Willowing Machine (CYLKS-1500 x2, CYLJM-1800 x2, CYLKS-1500 x2): These machines further open and clean the fibers, removing dust, dirt, and impurities, which is critical for filter material quality.
- Cabinet Blending Hopper (CYLMX-1800 x2): Here, different types of fibers might be blended in precise ratios to achieve the desired filtration properties. For example, some fibers might be better at capturing small particles, while others offer strength or chemical resistance.
- Carding Machine (CYLSL/II-2000 x2): This machine aligns the opened and blended fibers into a thin, continuous web, making them parallel and organized. This web forms the base structure of the filter material.
- Cross Lapper (YBG102-200×260 x2): The carded web is layered back and forth to build up thickness and width, creating a thicker, wider web.2 This is essential for filter materials needing depth for effective filtration.
- Winding Machine (LYBG102-260 x1): This machine winds the layered web onto rolls for easier handling and further processing.
- Feeding Machine (YBG301-260 x1): This ensures a consistent and controlled flow of the layered web into the needle punching machines.
- Preliminary Needle Punching Machine (YBG201D-260 x1): This machine starts the needle punching process, lightly entangling the fibers for better handling and cohesion.
- Needle Punching Machines (YBG202D-260 x4, YBG211D-260 x4): These machines with barbed needles further entangle the fibers, creating a strong, felt-like fabric structure. Multiple needle punching machines allow for varying degrees of entanglement and fabric density, which directly impacts the filtration efficiency.
- Cutting & Winding Machine (YBG422-260 x1): This machine cuts the wide rolls of needle-punched fabric into smaller rolls of specific widths for packaging and sale.
- Control Cabinet: This houses the electrical controls and systems to operate and monitor the entire production line.
Why Needle Punching for Filter Material?
Needle punching is a common method for creating non-woven filter materials because:
- Depth Filtration: The entangled fibers create a 3D structure that can trap particles throughout the fabric’s thickness, not just on the surface.3
- Variety of Densities: The degree of needle punching can be adjusted to create filters with different pore sizes and filtration efficiencies.
- Strength and Durability: Needle punching provides good mechanical strength to the filter material.4
- Versatility: It can be used with various fiber types to achieve specific filtration properties.
Types of Filter Materials Made on this Line:
This line can produce various filter materials depending on the fiber types and the needle punching parameters. These could include:
- Air Filters: For HVAC systems, automotive applications, and respirators.
- Liquid Filters: For water purification, industrial processes, and medical applications.
- Oil Filters: For engines and hydraulic systems.
In Simple Terms:
This production line takes raw fibers, cleans them thoroughly, blends them (if needed), aligns them into a web, layers the web for thickness, and then uses needles to entangle the fibers into a strong, three-dimensional fabric. This fabric is then turned into rolls of filter material designed to trap particles from air or liquids.
This configuration allows for the efficient production of high-quality non-woven filter materials tailored to specific filtration needs. The multiple needle punching machines provide flexibility for different filter grades and efficiencies.