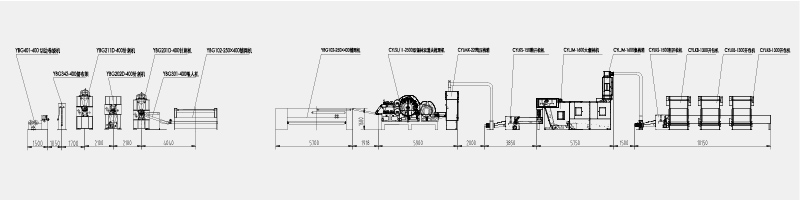
NON-WOVEN PRODUCTION LINE FOR PU BASE FABRIC | |||
TYPE | MAIN PARAMETER | NOTE | |
LYBG103 | carding output width | 2500mm | available for the materials of PSF/PHT/PPF/PPTA/NYLON (D1.5~10.0mm/L38.0~76.0mm) |
lapping output width | 4000mm | ||
finished products width | 3600mm | ||
material weight | 150~2000g/m² | ||
production speed | 0.5~6 m/min | ||
production output | 500kg/h | ||
power capacity | 184kw |
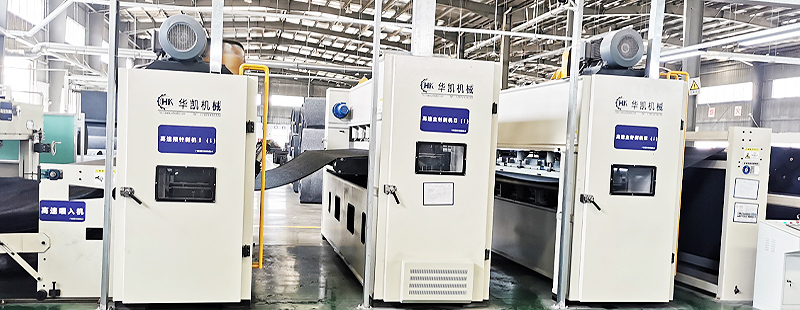
Production Line Configuration | ||||
NO. | MACHINERY | TYPE | QUANTITY | NOTE |
1 | Bale Opener | CYLKB-1300 | 3 | |
2 | Willowing Machine | CYLKS-1500 | 1 | |
3 | Willowing Machine | CYLJM-1600 | 1 | |
4 | Willowing Machine | CYLKS-1500 | 1 | |
5 | Cabinet Blending Hopper | CYLMX-2200 | 1 | |
6 | Carding Machine | CYLSL/II-2500 | 1 | |
7 | Cross Lapper | YBG102-250×400 | 1 | |
8 | Feeding Machine | YBG301-400 | 1 | |
9 | Preliminary Needle Punching Machine | YBG201D-400 | 1 | |
10 | Needle Punching Machine | YBG202D-400 | 1 | |
11 | Needle Punching Machine | YBG211D-400 | 1 | |
12 | Storage Rack | YBG342-400 | 1 | |
13 | Cutting & Winding Machine | YBG401-400 | 1 | |
14 | Control Cabinet | 1 | ||
15 | Bale Opener | CYLKB-400 | 1 | option |
non-woven production line designed for PU (Polyurethane) base fabric. Let’s break down what that means and what each machine contributes.
Understanding PU Base Fabric
PU base fabric refers to a non-woven material that will be coated or impregnated with polyurethane.1 This creates a composite material with the flexibility and strength of the non-woven fabric, combined with the protective and versatile properties of polyurethane.2 Think of it like a canvas that’s getting a special coating to make it waterproof, more durable, or give it a specific texture.
The Production Line Configuration
This list details the machinery, their models, quantities, and their roles in creating the PU base fabric.
- Bale Opener (CYLKB-1300 x3, CYLKB-400 x1 optional): This machine, as discussed before, loosens and opens compacted bales of raw fibers (likely polyester or polypropylene for PU base fabrics). The optional smaller bale opener might be for specialty fibers or smaller production runs.
- Willowing Machine (CYLKS-1500 x2, CYLJM-1600 x1): These machines further open and clean the fibers after the bale opener, removing dust, dirt, and impurities.
- Cabinet Blending Hopper (CYLMX-2200 x1): This is where different types of fibers (if needed) are mixed in precise ratios to achieve the desired properties in the base fabric.
- Carding Machine (CYLSL/II-2500 x1): This machine aligns the opened and blended fibers into a thin, continuous web, making them parallel and organized.
- Cross Lapper (YBG102-250×400 x1): The carded web is layered back and forth to build up thickness and width, creating a thicker, wider web.3
- Feeding Machine (YBG301-400 x1): This ensures a consistent and controlled flow of the layered web into the needle punching machines.
- Preliminary Needle Punching Machine (YBG201D-400 x1): This machine starts the needle punching process, lightly entangling the fibers for better handling and cohesion.
- Needle Punching Machines (YBG202D-400 x1, YBG211D-400 x1): These machines with barbed needles further entangle the fibers, creating a strong, felt-like fabric structure.4 Multiple needle punching machines allow for varying degrees of entanglement and fabric density.
- Storage Rack (YBG342-400 x1): This rack stores the large rolls of the finished needle-punched base fabric.
- Cutting & Winding Machine (YBG401-400 x1): This machine cuts the wide rolls of base fabric into smaller rolls of specific widths for packaging and sale.
- Control Cabinet: This houses the electrical controls and systems to operate and monitor the entire production line.
What Happens After the Base Fabric is Made?
The non-woven fabric produced by this line is the base for the final product. It will then undergo further processing, which is not included in this configuration:
- PU Coating/Impregnation: The fabric will be coated or impregnated with polyurethane.5 This process can involve various techniques depending on the desired properties of the final material.
- Drying/Curing: The PU-coated fabric will likely need to be dried or cured to solidify the polyurethane.
- Finishing: Additional finishing steps might be applied, such as embossing, printing, or surface treatments.
Uses of PU Coated Non-Wovens:
PU-coated non-wovens are used in a wide range of applications, including:
- Synthetic Leather: Used in upholstery, footwear, and apparel.
- Protective Clothing: Providing water resistance and durability.6
- Medical Textiles: For barrier properties and comfort.7
- Automotive Interiors: For durability and aesthetics.
- Industrial Applications: For filtration and other specialized needs.
In Simple Terms:
This production line creates the “foundation” fabric that will be enhanced with a polyurethane coating. Think of it like making a cake base before adding frosting and decorations. The base fabric provides the structure, while the PU coating adds the desired properties and functionality.
This configuration allows for the efficient production of a high-quality non-woven base fabric specifically designed for PU coating and subsequent use in a variety of applications.